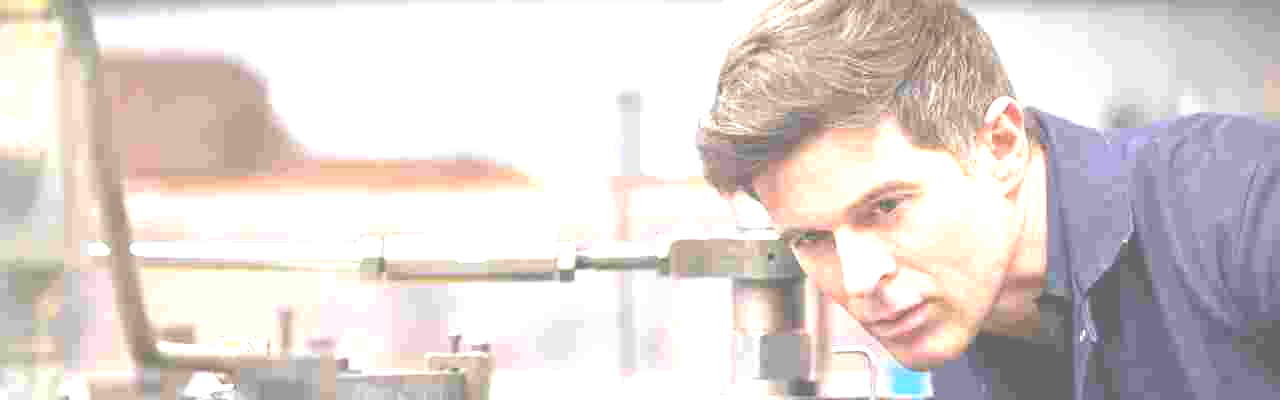

Резка сверхтвердых материалов
Дополнительная информация по услуге: Резка сверхтвердых материалов
- Описание
- Стоимость
- Примеры работ (фото, видео)
- Исполнители
- Оборудование
- ГОСТы
Разместить заказ
Выбрать исполнителя
Резка сверхтвердых материалов:
методы, особенности и рекомендации
Резка сверхтвердых материалов - комплекс технологических процессов, направленных на точное разделение или формирование заготовок и изделий из материалов, обладающих высокой твердостью и износостойкостью (алмазы, кубический нитрид бора, карбид вольфрама, корунд и т. д.).
В металлической промышленности сверхтвердые материалы нередко применяют для изготовления режущего инструмента (включая алмазный), а также деталей, подвергающихся экстремальным нагрузкам и работе в агрессивных средах. Правильный выбор метода и оборудования для резки данных материалов обеспечивает высокую точность, минимальное термическое и механическое воздействие и высокий ресурс инструмента.
Основные особенности сверхтвердых материалов
- Высокая твердость. Твердость по шкале Мооса находится в верхней части шкалы (8, 9 и даже 10), из-за чего обработка такими материалами требует особого подхода и применения специального инструмента.
- Износостойкость. Сверхтвердые материалы очень плохо поддаются традиционным методам обработки, так как режущий инструмент быстро изнашивается.
- Хрупкость. Несмотря на высокую твердость, многие сверхтвердые материалы (например, керамика и некоторые композиционные материалы) достаточно хрупкие. Резка при избыточных вибрациях или некорректном режиме может привести к микротрещинам и сколам.
- Низкая теплопроводность. Некоторые сверхтвердые материалы имеют низкую теплопроводность, что требует дополнительного охлаждения для предотвращения локального перегрева.
Основные методы резки сверхтвердых материалов
Алмазная резка
Принцип: использование инструмента с алмазным зерном (алмазные диски, фрезы, отрезные круги). Алмаз является самым твердым природным материалом, благодаря чему он способен эффективно резать металлы и сверхтвердые сплавы.
Преимущества: высокая точность и чистота реза, относительно «холодная» обработка, снижающая риск термических повреждений.
Недостатки: высокая стоимость алмазного инструмента, необходимость постоянного охлаждения (система СОЖ или подача воды), иначе алмаз быстро изнашивается.
Электроэрозионная резка (EDM)
Принцип: использование электрических разрядов, которые «выжигают» или «выкрашивают» мельчайшие частицы материала. Применяется либо проволочная электроэрозия, либо электроэрозионная прошивка (с помощью электрод-инструмента).
Преимущества: практически отсутствуют механические нагрузки на обрабатываемую деталь, возможность обрабатывать материалы любой твердости при условии, что они электропроводны (карбид вольфрама, металлокерамика, сплавы с добавками алмазной крошки и т. д.), высокая точность (до нескольких микрон).
Недостатки: подходит только для электропроводных материалов, низкая скорость резки по сравнению с некоторыми механическими методами, сложность оборудования и высокая стоимость.
Лазерная резка
Принцип: сфокусированный луч высокой мощности (чаще всего CO₂-лазер или твердотельный волоконный лазер) испаряет или расплавляет материал в точке воздействия.
Преимущества: высокая скорость резания, особенно при тонком листовом материале или небольших заготовках, безконтактный метод, что сокращает риски механических деформаций и вибраций, возможность автоматизации процесса.
Недостатки:
могут возникать термические деформации на границах реза при недостаточном охлаждении, так как лазер создает высокую температуру в точке воздействия; в случае резки очень толстых сверхтвердых деталей лазерная мощность должна быть очень высокой, что ведет к существенным затратам электроэнергии и усложняет оборудование; не все сверхтвердые материалы хорошо поглощают лазерное излучение (например, некоторые прозрачные для определенной длины волны материалы).
Гидроабразивная резка (waterjet)
Принцип: струя воды, смешанная с абразивными частицами (обычно гранат), подается под ультравысоким давлением (до 4000 бар и более) и механически вымывает узкую канавку в материале.
Преимущества: практически отсутствует тепловая нагрузка на материал, возможность обработки широкого спектра материалов, включая хрупкие и композитные (даже керамику и стекло), высокая точность и качество кромки.
Недостатки: высокая стоимость оборудования и расходных материалов (абразив), ограниченная скорость резки при увеличении толщины заготовки, необходимость иметь промышленный водопровод и систему очистки воды.
Ультразвуковая резка
Принцип: резание или шлифование при помощи высокочастотных колебаний. Часто ультразвук применяется в сочетании с абразивными суспензиями (ультразвуковая шлифовка, ультразвуковая ерозия).
Преимущества: низкие механические нагрузки и нагрев, что особенно актуально для хрупких сверхтвердых материалов (керамика, стекло и т. д.); высокая точность обработки сложных контуров.
Недостатки: низкая производительность по сравнению с другими методами, дорогое и сложное в обслуживании оборудование.
Критерии выбора метода резки
- Тип материала. Электропроводность (для EDM), теплопроводность (для лазера), толщина и хрупкость (для гидроабразива и ультразвука).
- Требуемая точность. Алмазная резка, EDM и ультразвук обеспечивают высокую точность, в то время как лазерная и гидроабразивная резка чаще используются при более массовом производстве и заготовках сложной формы.
- Производительность. При серийном выпуске часто важна скорость обработки. Лазер и гидроабразив обладают высокой скоростью, но это зависит от мощности оборудования и толщины материала.
- Экономическая целесообразность. Нужно учитывать стоимость инструмента, энергозатраты, расходные материалы и обслуживание оборудования.
Технологические рекомендации
При работе со сверхтвердыми материалами очень важно эффективно отводить тепло из зоны резания. Используются различные системы СОЖ, водное охлаждение, подвод абразивного раствора и т. д. Правильный выбор скорости резания, подачи, глубины реза и давления (в случае водяной струи) позволяет снизить износ инструмента и избежать повреждений детали.
Любые вибрации или лишние колебания приводят к ухудшению качества реза и сокращению ресурса инструмента.Для гидроабразивной резки, а также алмазного инструмента важны фракция абразива, его чистота и соответствие нормам по твердости.
Области применения
- Производство режущего инструмента (алмазные круги, сверла, фрезы): заготовки из кубического нитрида бора и карбида вольфрама нуждаются в высокоточной резке.
- Аэрокосмическая промышленность: изготовление деталей из жаропрочных и керамических материалов.
- Автомобильная промышленность: механизмы и узлы, работающие при высоких нагрузках и износах (например, детали топливной системы, инжекторы).
- Ювелирная индустрия: обработка алмазов и других драгоценных камней.
- Электроника: режущие инструменты для кристаллов (кремний, карбид кремния и т. д.), заготовки для подложек в микросхемах.
Резка сверхтвердых материалов – сложный технологический процесс, требующий специализированного оборудования, инструмента и соответствующего опыта у оператора. Правильный выбор метода и точная настройка режимов позволяют не только добиться высокого качества кромки, но и сэкономить на ремонте и замене инструмента, а также снизить брак.
Среди наиболее популярных способов можно выделить алмазную резку, электроэрозионную обработку, лазерные технологии, гидроабразивные и ультразвуковые методы. При этом каждый из них имеет свои плюсы и минусы и подбирается индивидуально в зависимости от свойств обрабатываемого материала, конечных требований к изделию и экономической целесообразности.
Материал | Стоимость, руб./пог. мм | |||
---|---|---|---|---|
Керамика (оксид алюминия, циркония) |
от 15 | |||
Карбид вольфрама | от 25 | |||
Стеклокерамика | от 10 | |||
Сапфир | от 30 | |||
Гранит | от 5 | |||
Кварцевое стекло | от 12 | |||
Алмаз | по запросу | |||
Композитные материалы | от 20 | |||
Нитрид кремния | от 22 | |||
Сверхтвердые сплавы | от 20 | |||
Титановые сплавы | от 18 | |||
Инструментальная сталь | от 15 |
Автор данного ролика представлен в нашем каталоге:
_