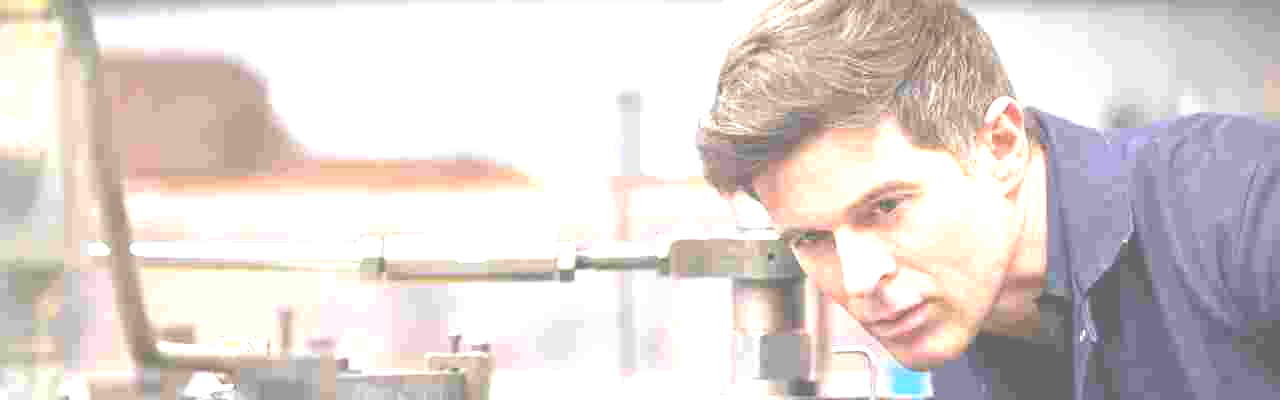

Закалочные ванны
Дополнительная информация по оборудованию: Закалочные ванны
- Описание
- Стоимость
- Примеры работ (фото, видео)
- Изготовители
- Применение
- ГОСТы
Разместить заказ
Выбрать исполнителя
Закалочные ванны:
назначение, применение и выбор охлаждающей среды
Закалочные ванны – один из ключевых элементов технологического процесса термической обработки металлов, в частности, процедуры закалки. Основная задача таких ванн заключается в быстром и равномерном охлаждении раскалённой заготовки до нужной температуры, позволяющем достичь требуемых механических свойств металла (прежде всего – твёрдости и прочности). Ниже мы рассмотрим, как устроены закалочные ванны, как они применяются на производстве и каков их вклад в общее качество металлопродукции.
Назначение и суть закалки
Закалка – это термическая операция, в ходе которой металл (обычно сталь, но могут быть и другие сплавы) нагревают до определённой температуры выше критической точки и затем резко охлаждают в соответствующей среде (масло, вода, полимерные растворы и т.д.). Такая обработка позволяет получить мартенситную или другую твёрдую структуру с высокой твёрдостью и износостойкостью.
Однако после закалки металл может быть слишком хрупким, поэтому зачастую её совмещают с последующим отпуском (дополнительным нагревом до более низкой температуры). Это придаёт металлу сочетание твёрдости, пластичности и ударной вязкости.
Роль закалочных ванн
Закалочная ванна обеспечивает равномерное и контролируемое охлаждение заготовки. Применение специализированных ванн даёт возможность:
- точно поддерживать температуру охлаждающей среды;
- регулировать скорость охлаждения;
- обеспечивать одинаковые условия охлаждения для каждой детали, что критически важно для массового производства, где требуется воспроизводимость свойств изделий.
Конструкция и основные элементы закалочных ванн
Закалочные ванны могут значительно варьироваться по размерам, конструктивным особенностям и типу применяемого охлаждающего состава, однако базовая схема обычно включает следующие элементы:
- корпус ванны. Изготавливается из металла, стойкого к воздействию охлаждающих жидкостей и перепадам температур. Может иметь дополнительные теплоизоляционные слои или специальные кожухи, чтобы минимизировать потери тепла/холода и обеспечивать энергоэффективность;
- система нагрева или охлаждения жидкости. Несмотря на название «закалочная ванна», в некоторых случаях бывает необходимо поддерживать строго определённую (или даже повышенную) температуру закалочной среды – например, в масляных ваннах оптимально выдерживать 50–80 °C. С этой целью в конструкции могут присутствовать нагревательные элементы или системы теплообмена (теплообменники);
- система циркуляции и фильтрации для получения равномерного охлаждения необходима циркуляция жидкости внутри ванны. Это может обеспечиваться насосами либо механическими мешалками. Фильтрация жидкости нужна для удаления продуктов окисления, окалины, металлической стружки, а также для поддержания чистоты среды. Загрязнённая жидкость снижает качество охлаждения;
- контрольно-измерительное оборудование. Датчики температуры, системы контроля уровня жидкости, а также в некоторых случаях датчики скорости потока среды. Эти инструменты позволяют оператору или автоматизированной системе поддерживать оптимальные условия для закалки;
- системы безопасности. Вентиляционные и вытяжные устройства для отвода паров и дыма (особенно актуально при масляных ваннах). Автоматические клапаны или аварийные системы выключения/слива для предотвращения перегрева, загорания масла или других внештатных ситуаций.
Виды охлаждающих сред в закалочных ваннах
Скорость охлаждения металла зависит от выбранного состава. Основные варианты:
- Водные растворы и вода. Вода – наиболее доступный и распространённый охладитель. Используется в случаях, когда нужна очень высокая скорость охлаждения. Недостаток – повышенный риск образования трещин из-за термических напряжений, а также коррозия;
- Масляные составы. Специальное закалочное масло обеспечивает более мягкое охлаждение по сравнению с водой. o Позволяет снизить риск растрескивания деталей, уменьшить коррозию. Требует строгого контроля температуры (обычно 50–80 °C) и системы пожаробезопасности;
- Полимерные (водополимерные) растворы. Представляют собой концентраты, которые разводятся водой. Скорость охлаждения регулируется концентрацией полимера: при увеличении концентрации скорость охлаждения снижается. Подходят для широкого спектра сталей и чугунов, могут обеспечивать более гибкую настройку процесса;
- Солевые расплавы. Обычно применяются при необходимости поддерживать высокие температуры охлаждающей среды (сотни градусов). Используются для специальных сталей, титановых и никелевых сплавов. Обеспечивают равномерность нагрева и охлаждения, но требуют строгого соблюдения техники безопасности;
- Газовая среда (для высокотехнологичных процессов). Чаще встречается в вакуумных печах. Формально это не «ванна», но принцип «среды для закалки» тот же – быстрое охлаждение, но уже под давлением газа (азот, гелий и др.). Обеспечивает минимальное окисление поверхности, но требует сложного оборудования и существенных затрат.
Технология использования закалочных ванн
- Подготовка ванны. Проверяют уровень и чистоту рабочей жидкости. Устанавливают (если необходимо) рабочую температуру, включая нагрев и циркуляцию. Настраивают скорость потока, фильтры, систему отвода паров (особенно важно при использовании масел).
- Нагрев металла. Перед погружением в ванну заготовка нагревается в печи до заданной температуры (выше критической точки Ac3 или Ac1 – в зависимости от типа стали и желаемой структуры). Деталь выдерживается при этой температуре определённое время для выравнивания структуры и завершения фазовых превращений.
- Погружение в закалочную ванну. Заготовку извлекают из печи и как можно быстрее (чтобы избежать охлаждения на воздухе) опускают в ванну. Время нахождения детали в ванне и режим охлаждения рассчитывают заранее. В некоторых случаях применяется метод «калиброванного времени» – деталь удерживают в жидкости ровно столько, сколько необходимо для достижения нужной структуры, а затем вынимают для дальнейшей обработки.
- Дальнейшая обработка. После закалки заготовка может направляться на отпуск (дополнительный нагрев до более низкой температуры) для снижения внутреннего напряжения и повышения пластичности. При масляном закаливании деталь часто промывают от остатков масла. Контроль качества предполагает проверку твёрдости, структуры и геометрических размеров.
Где и как применяются закалочные ванны?
- Металлообрабатывающие предприятия и кузнечно-прессовые цеха. Массовое производство деталей (шестерни, валы, оси, инструменты). Закалочные ванны здесь идут в комплекте с печами и другими установками термообработки.
- Станкостроение. Изготовление и ремонт станочных узлов (например, направляющих, шпинделей, резьбонарезных элементов). Закалка позволяет повысить твёрдость и износостойкость деталей, с которыми идёт постоянный контакт при работе станка.
- Автомобильная и авиационная промышленность. Производство коленвалов, распредвалов, шестерён КПП, деталей подвески и т.д. Высокие требования к прочности и надёжности обуславливают применение специализированных закалочных линий с автоматизированным контролем.
- Нефтегазовая отрасль. Детали бурового оборудования, насосно-компрессорные трубы, инструменты для работы в агрессивных средах. Закалка повышает устойчивость к абразивному износу и ударным нагрузкам.
- Производство инструментов. Сверла, фрезы, резцы, пилы и другие режущие инструменты нуждаются в высокой твёрдости для эффективной работы по металлу и дереву. Закалочные ванны позволяют получать однородную структуру инструмента и обеспечивать долговечность.
- Сельскохозяйственная и строительная техника. Закалке подвергают рабочие органы машин: ножи, лемехи, ковши экскаваторов, гидроцилиндры. Важно сочетание твёрдости (для износостойкости) и вязкости (чтобы избежать поломок при ударных нагрузках).
Выбор закалочной ванны: основные критерии
Для углеродистых сталей средней твёрдости зачастую достаточно водных ванн. Легированные или высокоуглеродистые сплавы могут нуждаться в масляной или полимерной среде. Большие детали требуют вместительных ванн с мощной системой циркуляции. Для тонкостенных заготовок важно максимально ровное и щадящее охлаждение, чтобы снизить деформации.
В серийном производстве предпочтительны автоматические закалочные линии со стабильным циклом термообработки. Небольшие мастерские нередко используют компактные ванны без сложных систем контроля. Масляная ванна требует продуманных мер пожарной безопасности и систем очистки. Полимерные растворы требуют контроля концентрации, но более безопасны и меньше дымят.
Если важна чистота и отсутствие окислов, могут применяться вакуумные системы или полимерные составы. Для заготовок, которые впоследствии шлифуются или полируются, критично минимизировать образование окалины и трещин.
Основные преимущества применения закалочных ванн
- Повышение твёрдости и износостойкости деталей.
- Универсальность: возможность настройки под различные типы сталей и сплавов.
- Повышенная воспроизводимость при массовом производстве, благодаря автоматическому поддержанию параметров.
- Экономическая эффективность: при правильном подборе среды и конструкции системы можно снизить брак и исключить повторные операции.
- Безопасность и экологичность (при соблюдении норм) – современные ванны снабжаются эффективными системами улавливания дыма, фильтрации, контроля температуры.
Закалочные ванны – незаменимый элемент во многих областях металлообработки и станкостроения. Они обеспечивают быстрое и контролируемое охлаждение детали, что является ключом к получению требуемых механических свойств металла (твёрдости, прочности, износостойкости и т.д.).
Правильный выбор типа закалочной среды и оборудования позволяет оптимизировать технологический процесс, добиться высоких показателей надёжности изделий, а также обеспечить конкурентоспособность производства.
Приобретая или модернизируя закалочную ванну, предприятия должны учитывать тип обрабатываемой стали, производственные объёмы, требования к безопасности и экологии, а также необходимость в автоматизации процессов. Грамотно подобранное и установленное оборудование способно существенно повысить качество выпускаемой продукции и снизить издержки за счёт уменьшения брака и повышения эффективности термообработки.
Если вы планируете внедрять или улучшать процесс закалки на своём предприятии, внимательно проанализируйте потребности, изучите характеристики доступных охлаждающих сред и проконсультируйтесь со специалистами. Такой комплексный подход позволит максимально раскрыть преимущества, которые дают закалочные ванны в современной металлообработке.
Тип ванны | Стоимость, тыс. руб. | |||
---|---|---|---|---|
Малая (углеродистая сталь) |
от 30 | |||
Малая (нержавеющая сталь) | от 50 | |||
Средних размеров (углеродистая сталь) | от 70 | |||
Средних размеров (нержавеющая сталь) | от 100 | |||
С системой охлаждения (углеродистая сталь) | от 150 | |||
С системой охлаждения (нержавеющая сталь) | от 200 | |||
С мешалкой (углеродистая сталь) | от 120 | |||
С мешалкой (нержавеющая сталь) | от 170 | |||
С системой нагрева и охлаждения (углеродистая сталь) | от 250 | |||
С системой нагрева охлаждения (нержавеющая сталь) | от 350 |
Автор данного ролика представлен в нашем каталоге:
_