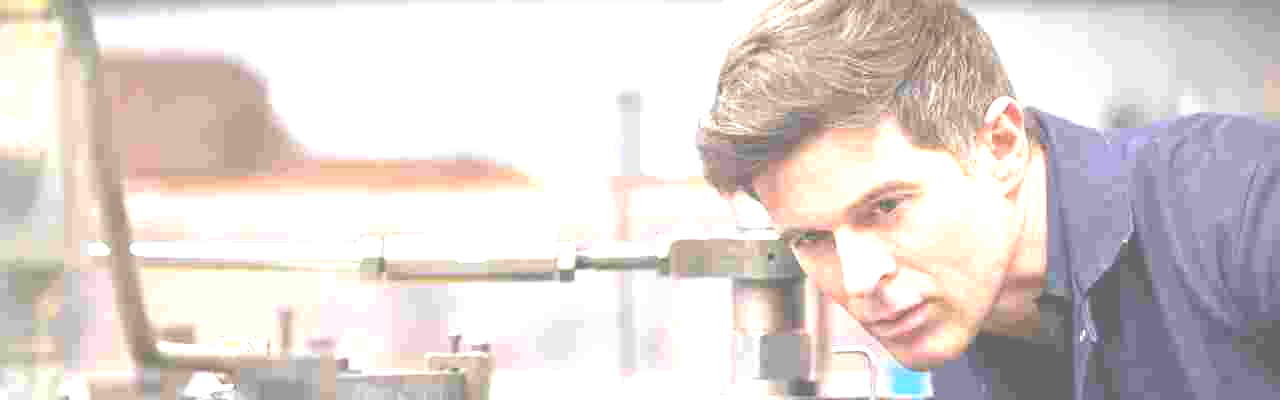

Все услуги
› Изготовление деталей › Изготовление деталей разных типов › Изготовление плунжеров
показать все ▼
Изготовление плунжеров
Дополнительная информация по услуге: Изготовление плунжеров
- Описание
- Стоимость
- Примеры работ (фото, видео)
- Исполнители
- Оборудование
- ГОСТы
Разместить заказ
Выбрать исполнителя
Плунжер: что это такое,
материалы, изготовление и применение
Плунжер – шток или поршень цилиндрической формы, выполняющий возвратно-поступательные движения в гидравлических, топливных, насосных и иных механизмах. Основная задача плунжера – преобразование давления жидкости или газа в механическую работу (или наоборот, передачи движения на рабочую жидкость).
Области применения плунжеров:
- гидравлические системы – гидроцилиндры, прессы, подъёмники;
- топливная аппаратура – топливные насосы высокого давления в двигателях внутреннего сгорания;
- насосное оборудование – плунжерные насосы для перекачки вязких или агрессивных жидкостей;
- пневматические системы – пневмоцилиндры, пневмопоршни.
От надёжности и точности изготовления плунжера во многом зависит эффективность, долговечность и герметичность работы оборудования. Нередко к плунжерам предъявляются строгие требования по шероховатости и геометрической точности.
Основные материалы для изготовления плунжеров
Для производства плунжеров используют материалы с высокой износостойкостью и прочностью. Также важно обеспечить хорошую сопротивляемость коррозии и усталостным нагрузкам. Наиболее распространённые варианты:
- углеродистые и легированные стали. Например, сталь 40Х, 45, 38ХН3М. Отличаются хорошими механическими характеристиками, допускают закалку и последующую термообработку;
- нержавеющие стали. AISI 304, 316, 420 и аналогичные марки, применяются там, где требуется повышенная коррозионная стойкость (морская вода, агрессивные среды);
- инструментальные стали. Применяются в особо нагруженных, высокоточных механизмах (топливные насосы высокого давления). Позволяют достигать высоких значений твёрдости при правильной термообработке;
- сплавы на основе меди, алюминия и титана. Используются реже, в специфических задачах с учётом требований по весу, теплопроводности и прочности.
Выбор материала зависит от условий эксплуатации, давления, требуемого ресурса и экономической целесообразности.
Технологический процесс изготовления плунжеров
Процесс изготовления плунжера можно условно разделить на несколько ключевых этапов. К предварительным относятся:
- проектирование и подготовка технической документации. Расчёт конструкции: определение диаметра плунжера, длины рабочего хода и запаса прочности. Учёт условий эксплуатации: рабочая температура, давление, характер нагрузки;
- выбор материала с учётом коррозионной стойкости, твёрдости и возможности термообработки;
- разработка чертежей и 3D-моделей. Создание технической документации с указанием допусков, шероховатости и видов покрытий;
- выбор заготовки. Используются круглый прокат, поковки или прутки. Диаметр и длина заготовки должны обеспечивать минимальный припуск на обработку;
- подготовительные операции. Резка заготовок на нужную длину. Возможна черновая токарная обработка для удаления лишнего материала и получения приблизительной формы.
Чистовая механическая обработка включает:
- токарную обработку. Создание основного цилиндрического тела, обработка торцов, проточка канавок, формирование посадочных мест под уплотнительные элементы;
- фрезерную обработку (при необходимости) - при сложной геометрии плунжера (например, шпоночный паз или технологические отверстия);
- шлифование для достижения высокой степени точности по диаметру и минимальной шероховатости поверхности;
- хонингование или суперфиниш. Применяется в тех случаях, когда требуется особо точное соответствие по диаметру и низкие показатели шероховатости (Ra ≤ 0,2 мкм).
Термическая или химико-термическая обработка
Закалка и отпуск применяются для сталей (например, 40Х, 38ХН3М) для повышения твёрдости, износостойкости и выносливости. Нитроцементация, азотирование, цементация - химико-термические процессы, повышающие поверхностную твёрдость без значительного увеличения хрупкости. При работе с агрессивными средами или в условиях высоких нагрузок могут дополнительно наноситься упрочняющие покрытия (например, хромирование, DLC-покрытие и др.).
Финальная обработка и контроль качества
- Сверхточное шлифование, полирование для получения окончательных параметров поверхности;
- контроль геометрии - измерение диаметра, длины, проверка соосности, отсутствие эллипсности;
- контроль шероховатости с использованием профилометра или других методов неразрушающего контроля;
- контроль твёрдости. Замеры по шкалам HRC, HV или другим стандартам для подтверждения заданных характеристик.
Ключевые факторы качества
Плунжер должен иметь строгие допуски по диаметру, торцевому биению, соосности и форме. Любые отклонения могут привести к утечкам рабочей жидкости и быстрому износу. В зоне уплотнений критически важна шероховатость. Чем она ниже, тем выше герметичность и меньше трение. Твёрдость и износостойкость достигаются грамотным выбором стали, правильным проведением закалки, отпуска и возможного химико-термического упрочнения. Коррозионная стойкость рекомендуется в условиях влажной или агрессивной среды. Для этого используют специальные марки сталей или защитные покрытия.
Перед монтажом плунжер должен быть очищен от технологических загрязнений, следов СОЖ и металлической пыли. При хранении – защищён от коррозии специальной смазкой или маслом.
Производство в условиях серийного и единичного изготовления
Особенности серийного производства - автоматизация процессов (ЧПУ-станки, роботизированные участки), оптимизация технологических операций и использование конвейерных линий, упор на минимизацию себестоимости при сохранении качества. Единичного и мелкосерийного - индивидуальный подход к каждому заказу, гибкость выбора материалов и процессов, возможность быстрой корректировки конструкции и технологии по требованиям заказчика, а также более высокие затраты на единицу продукции. Но точность и уникальность работы в этом случае выше.
Современные тенденции и перспективы
- Использование 3D-печати металлом. Пока не слишком распространено для изготовления плунжеров, однако перспективно для производства сложных форм или при необходимости быстрой замены деталей;
- нанесение инновационных покрытий - DLC (алмазоподобное углеродное покрытие), PVD (физическое осаждение из газовой фазы) и другие методы, обеспечивающие крайне высокую износостойкость и антифрикционные свойства;
- автоматизация измерений и контроля. Внедрение систем машинного зрения, высокоточных координатно-измерительных машин (CMM) для быстрой и точной проверки параметров;
- использование улучшенных сталей. Специально разработанные сорта с оптимальным сочетанием твёрдости, коррозионной стойкости и обрабатываемости.
Изготовление плунжеров – многоэтапный технологический процесс, требующий высокой квалификации специалистов и строгого соблюдения стандартов качества. Правильный выбор материала, точная мехобработка, грамотная термообработка и контроль на каждом этапе позволяют добиться требуемой геометрической точности, износостойкости и герметичности.
При разработке плунжеров важно учитывать условия эксплуатации и характер нагрузки, чтобы обеспечить оптимальный запас прочности и длительный срок службы детали. Развитие технологий – от современной металлургии до автоматизации производственных процессов – открывает новые возможности в создании плунжеров с улучшенными характеристиками для самых сложных задач в металлургической, нефтегазовой, автомобильной и других отраслях промышленности.
Если требуется изготовить партию плунжеров или разработать индивидуальные решения для особых условий работы, стоит обратиться к профессионалам, располагающим современным оборудованием и опытом производства высокоточных деталей.
Тип плунжера | Стоимость, руб. | |||
---|---|---|---|---|
Стандартный цилиндрический |
от 500 | |||
С канавками | от 800 | |||
С резьбой | от 1000 | |||
С отверстиями | от 1200 | |||
Нестандартный | от 1500 | |||
С закалкой | от 1800 | |||
С полировкой (шлифовкой) | от 2000 | |||
С покрытием | от 2200 | |||
Мини-плунжер | от 3000 |
Автор данного ролика представлен в нашем каталоге:
_