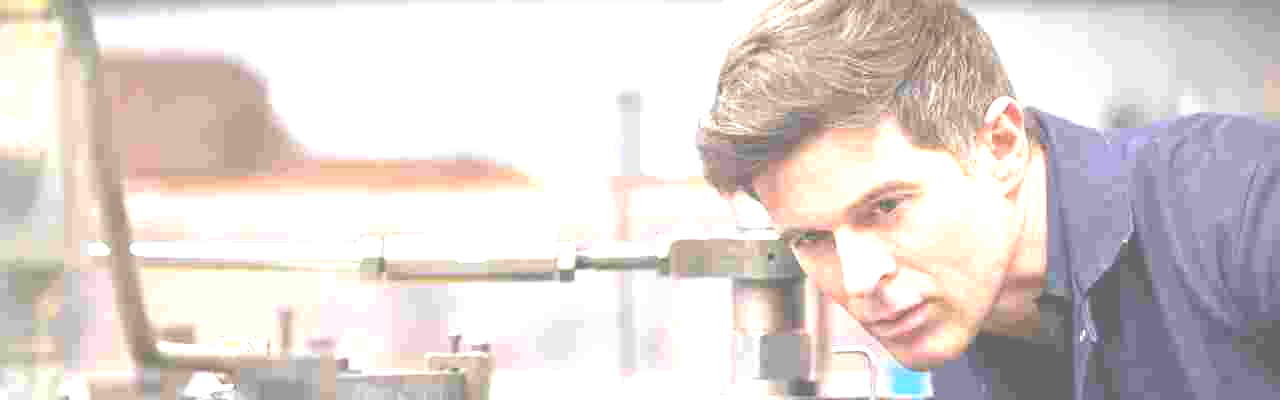

Лазерное термоупрочнение
Дополнительная информация по услуге: Лазерное термоупрочнение
- Описание
- Стоимость
- Примеры работ (фото, видео)
- Исполнители
- Оборудование
- ГОСТы
Разместить заказ
Выбрать исполнителя
Лазерное термоупрочнение:
световая броня для ваших деталей
Время – безжалостный враг любого металла. Но не стоит сдаваться, ведь современные технологии способны намного продлить жизнь любой заготовки или детали. Один из проверенных способов сделать это - закалка лазером. Она помогает создать на поверхности невидимый барьер, способный предотвратить не только ржавление, но и естественный износ и усталость материала. Суть лазерной закалки металла
В теории металлообработки этот процесс больше известен как лазерное термоупрочнение металла. А сводится он к трем этапам. На первом осуществляется локальный нагрев детали: сфокусированный лазерный луч высокой мощности за доли секунды доводит поверхность металла до температуры закалки (+900-1300°C). Далее следует не менее быстрое охлаждение (со скоростью 1000-10000°C/сек), при котором наблюдается теплоотвод вглубь материала. В результате происходят изменения структуры: быстрое охлаждение приводит к образованию мартенсита - очень твердой и износостойкой формы.В качестве финишной операции после основной обработки можно использовать отпуск: нагрев закаленного участка до более низкой температуры (+200-500°C) с последующим медленным охлаждением. Это делается для повышения пластичности и ударной вязкости металла.
Преимущества лазерной закалки
От многих других видов термообработки лазерная закалка металлов отличается селективностью: луч работает только с заданным участком поверхности, не затрагивая остальных. Это исключает деформацию и изменение размеров детали, что особенно важно для обработки сложных и прецизионных изделий. То есть при необходимости можно закаливать не всё изделие а отдельные элементы с разными характеристиками.После обработки характеристики металла значительно улучшаются. Он приобретает:
- повышенную твердость - до 65 HRC, что в несколько раз больше твердости незакаленного. Это значительно увеличивает срок службы деталей;
- износостойкость - в 2-5 раз выше, чем для необработанного проката. Благодаря этому можно значительно снизить расходы на ремонт и замену деталей, а также повысить производительность оборудования, в котором они работают;
- стойкость к коррозии. Одно из важнейших качеств, особенно для металлоизделий, эксплуатирующихся в агрессивных средах;
- отсутствие деформации, что позволяет сохранить точность и геометрию деталей;
- экологичность. В отличие от других способов лазерная закалка стали и других материалов - процесс, полностью безопасный для окружающей среды и здоровья человека;
- высокая скорость, гарантирующая обработку больших партий деталей за короткое время.
Способы охлаждения
при лазерном термоупрочнении металла
После закалки лазером можно использовать разные виды мгновенного охлаждения. Самым простым, доступным и потому распространенным считается водяное. К нему обращаются для охлаждения крупных деталей, а также изделий из стали с низкой легированностью. Вода подается на поверхность струей или каскадом, обеспечивая высокую скорость процесса. Воздушное охлаждение подходит для небольших деталей, а также для изготовленных из высоколегированных сталей. Воздух подается на поверхность детали струей или при помощи вентилятора. Этот тип охлаждения проигрывает водяному в скорости.
Газовое охлаждение имеет очень узкую специфику применения: его выбирают для деталей из титановых сплавов и других материалов, чувствительных к термическому удару. В качестве охладителя применяется инертный газ (аргон или гелий). Это более щадящий процесс по сравнению с водяным и воздушным.
Чтобы совместить процедуры охлаждения и отпуска, при лазерном термоупрочнении металла используют и охлаждение в расплаве. Оно полезно для изделий, требующих высокой износостойкости и коррозионной стойкости. В процессе деталь погружают в расплав соли или металла, нагретый до заданной температуры. В этом случае обеспечиваются высокая твердость и равномерная структура закаленного слоя.
Самый специфичный способ - криогенное охлаждение, которым обрабатывают детали, требующие максимальной твердости и износостойкости. Рабочей средой становится жидкий азот температурой -196°C. Эта технология обеспечивает максимально высокую твердость и минимальную остаточную аустенитную фазу.
В целом выбор способа зависит от материала детали, от ее размеров и формы и от требуемых характеристик закаленного слоя
Оборудование лазерной закалки
Лазерную закалку металлов выполняют тремя типами лазеров: Nd:YAG, CO2 и волоконными. Наиболее универсальные Nd:YAG имеют длину волны 1064 нм и мощность 1-10 кВт. Отличаются хорошей производительностью, но дороги, и с помощью них не всегда можно достичь нужного эффекта закалки.CO2 лазеры с длиной волны 10,6 мкм и мощностью 1-5 кВт более эффективны, так как глубже проплавляют металл. Но именно поэтому не подходят для обработки тонких деталей. Волоконные лазеры с длиной волны 1064-1080 нм и мощностью, аналогичной CO2, компактны и экономичны по эксплуатационным расходам, но это самый дорогостоящий тип устройств.
Ограничения и риски
лазерной закалки металлов
Несмотря на универсальность, лазерная закалка стали и других металлов и сплавов все-таки имеет ограничения. и прежде всего по толщине: она позволяет упрочнять только поверхностный слой детали, который обычно составляет от 0,1 до 3 мм.Наилучшие результаты технология демонстрирует в обработке сталей, титановых и алюминиевых сплавов, а также многих видов чугунов. К группе риска относятся металлы с низкой теплопроводностью: медь, латунь, бронза, нержавейка и чугун с высоким содержанием графита. Еще одним “неудобством” технологии можно назвать трудности в обработке деталей со сложным рельефом: например, с внутренними полостями.
Перед тем как решиться на закалку лазером, следует учесть и возможные риски. При несоблюдении технологических параметров могут возникнуть такие дефекты, как трещины, поры, обезуглероживание, окисление. А вышеперечисленные детали с низкой теплопроводностью могут деформироваться под действием лазерного луча. Избежать проблем помогут качественная подготовка поверхности (удаление с нее загрязнений и окислов), а также соблюдение технологических параметров.
Закалка лазером - без трудностей и рисков
Чтобы технология лазерного упрочнения металла работала на вас, а не против вас, лучше обратиться к профессионалам. Специалисты наших предприятий имеют все необходимые знания и навыки, используют современное лазерное оборудование ведущих мировых производителей и предлагают:- комплексный подход с выбором оптимальных параметров обработки,
- строгий поэтапный контроль качества,
- конкурентные цены,
- комфортные сроки выполнения проектов,
- индивидуальный подход и консультации.
Тип услуги | Стоимость, тыс. руб./кв.м | |||
---|---|---|---|---|
Лазерная закалка стали | от 3 | |||
Лазерная закалка чугуна | от 4 | |||
Лазерная закалка цветных металлов | от 5 | |||
Лазерное упрочнение с легированием | от 6 | |||
Лазерное упрочнение с наноструктурированием |
от 7 |