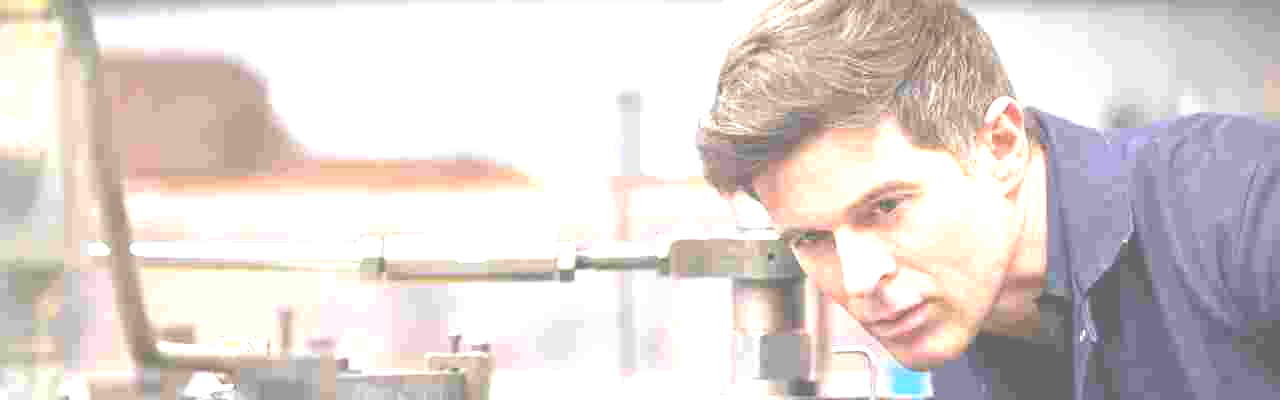

Ремонт насосов
Дополнительная информация по услуге: Ремонт насосов
- Описание
- Стоимость
- Примеры работ (фото, видео)
- Исполнители
- Оборудование
- ГОСТы
Разместить заказ
Выбрать исполнителя
Ремонт насосов в металлообработке:
диагностика, этапы и профилактика
Насосы широко применяются в металлообработке: они обеспечивают подачу охлаждающих жидкостей, смазочных материалов, масел и других технологических сред к станкам и агрегатам. От их исправной работы напрямую зависит стабильность производственных процессов, качество готовой продукции и уровень эксплуатационных затрат. Однако, как и любое промышленное оборудование, насосы подвержены износу и неисправностям.
Ниже рассмотрим основные причины поломок насосов, особенности диагностики, ремонтные мероприятия и профилактику для поддержания оборудования в рабочем состоянии.
Виды насосов и их применение в металлообработке
Центробежные
Часто используются для циркуляции охлаждающей жидкости в системах металлообработки: отвод стружки и эмульсии, охлаждение инструмента и детали. Имеют простую конструкцию и сравнительно высокую надёжность, поэтому их ремонт обычно не вызывает серьёзных затруднений.
Шестерёнчатые
Применяются для перекачки масел, гидравлических жидкостей и других вязких сред. При металлообработке они могут отвечать за подачу смазки в подшипниковые узлы либо в системы гидравлики станков. Из-за постоянной работы с густыми средами шестерёнчатые насосы подвержены износу зубчатых колёс и повышенным нагрузкам на уплотнения.
Поршневые
Часто встречаются в гидравлических прессах и испытательных стендах, где важно поддерживать высокое давление. Механизм таких насосов более сложен, чем у центробежных, и включает поршни, уплотнительные кольца, клапаны и штоки. Поломки обычно связаны с деформацией поршней и выходом из строя уплотнений.
Вакуумные
Используются там, где необходимо создавать и поддерживать вакуум для определённых технологических процессов (например, при сварке в вакууме или изготовлении вакуумных покрытий). Их неисправности могут быть связаны с утечками воздуха, перегревом или недостаточной смазкой.
Основные причины неисправностей
- Износ деталей. При интенсивной эксплуатации и высоких температурах элементы насоса – подшипники, уплотнения, шестерни, крыльчатки – подвергаются естественному износу. Металл со временем теряет необходимые механические свойства (твёрдость, прочность), что приводит к преждевременному выходу из строя рабочих узлов.
- Нарушение условий эксплуатации. Частая работа насоса «всухую» (без достаточной подачи жидкости), резкие перепады температур или превышение допустимого давления могут привести к поломке. Например, в металлообработке насосы порой испытывают чрезмерные нагрузки, если система подачи охлаждающей жидкости засоряется стружкой или другими примесями.
- Неправильный монтаж или неквалифицированное обслуживание. Установка насоса с несоосностью валов, несоблюдение технических зазоров или неправильно подобранные смазочные материалы способствуют возникновению вибраций и увеличивают вероятность поломок.
- Попадание посторонних предметов. Стружка, остатки абразива, частицы твёрдых материалов при некачественной фильтрации могут попадать в рабочую камеру насоса и повреждать внутренние элементы (лопасти крыльчатки, зубья шестерён, уплотнения).
Диагностика и инструменты для ремонта
Перед началом работ следует проверить целостность корпуса насоса и его основных узлов. Обратить внимание на наличие следов подтёков жидкости, трещин, сколов. Наличие постороннего шума или повышенной вибрации может указывать на износ подшипников, дефекты крыльчатки или небаланc ротора. В металлообработке, где насосы работают вблизи станков, слуховая диагностика иногда затруднена, поэтому предпочтительны измерительные приборы (виброметры).
Используя контрольно-измерительные приборы, можно сделать тесты на герметичность, давление и производительность, измерить радиальные и осевые люфты вала, проверить температуру подшипников, проанализировать состояние масла или смазочно-охлаждающей жидкости. Для ремонта насосов используют следущие инструменты:
- стандартный слесарно-монтажный набор (ключи, отвёртки, съёмники подшипников);
- специализированные приспособления (прессы для монтажа подшипников, плоскопараллельные плиты для проверки плоскостей, динамометрические ключи);
- средства для очистки и обезжиривания (растворители, ультразвуковые ванны, моечные машины высокого давления);
- ЗИП (запасные и быстроизнашивающиеся части): уплотнения, сальники, подшипники, прокладки, шестерни и т. д.
Этапы ремонта
- Разборка насоса. Снятие крышки, крыльчатки, ротора (или шестерён, поршней — в зависимости от типа насоса). Демонтаж подшипников и уплотнительных колец. Очистка и дефектовка всех деталей.
- Оценка состояния деталей. Проверка состояния лопаток, поршней, шестерён на наличие трещин, сколов, потертостей. Измерение геометрических параметров (толщины, диаметра, высоты зубьев). Обнаружение коррозии на металлических поверхностях.
- Замена и восстановление. Установка новых уплотнений, сальников, прокладок. Замена изношенных подшипников или шестерён (при наличии выработки зубьев). Возможна механическая обработка вала и посадочных мест (шлифовка, полировка или хромирование). Наплавка и восстановление геометрии деталей, если это экономически целесообразно.
- Сборка и тестирование. При сборке строго соблюдают технические зазоры и моменты затяжки крепежа. Проводят проверку на герметичность и отсутствие вибраций. Тестируют производительность (уровень расхода/давления). В металлообработке дополнительно отслеживают, насколько стабильно подаётся смазочно-охлаждающая жидкость или масло.
Профилактика и рекомендации по эксплуатации
Фильтры, сетки и системы охлаждения должны своевременно чиститься от стружки и других загрязнений. Чем лучше фильтрация, тем меньше риск повреждения внутренних элементов насоса. Рекомендуется использовать приборы учёта и сигнализации, которые отключают насос при превышении критических значений или при отсутствии подачи жидкости.
Грязное или отработанное масло приводит к ускоренному износу деталей и повышенной вибрации. Использование качественных смазок и масел – залог долгой службы оборудования. Регулярное техническое обслуживание позволяет обнаруживать начинающиеся проблемы (износ уплотнений, люфт вала, появление трещин) и устранять их до серьёзных поломок. Квалифицированные специалисты с необходимыми знаниями и навыками реже допускают ошибки при монтаже или эксплуатации насосов.
Ремонт насосов в условиях металлообработки требует комплексного подхода: точной диагностики, качественного подбора запасных частей и аккуратного проведения работ. Своевременное техническое обслуживание, соблюдение регламентов и правил эксплуатации помогают продлить ресурс насосного оборудования, снизить затраты на ремонт и обеспечить стабильность производственного процесса.
Внедрение современных методов контроля (вибродиагностика, тепловизионные исследования) и использование надёжных материалов для ремонта способны вывести работу насосов на новый уровень эффективности и надёжности.
Услуга | Стоимость, руб. | |||
---|---|---|---|---|
Диагностика насоса |
от 2500 | |||
Техническое обслуживание | от 5000 | |||
Ремонт гидравлической части | от 8000 | |||
Ремонт электрики | от 6000 | |||
Замена подшипников | от 4000 | |||
Замена уплотнений | от 3000 | |||
Восстановление вала | от 10000 | |||
Замена муфты (по необходимости) | от 3000 | |||
Балансировка ротора | от 5000 | |||
Пуско-наладочные работы | от 3000 |
Автор данного ролика представлен в нашем каталоге:
_