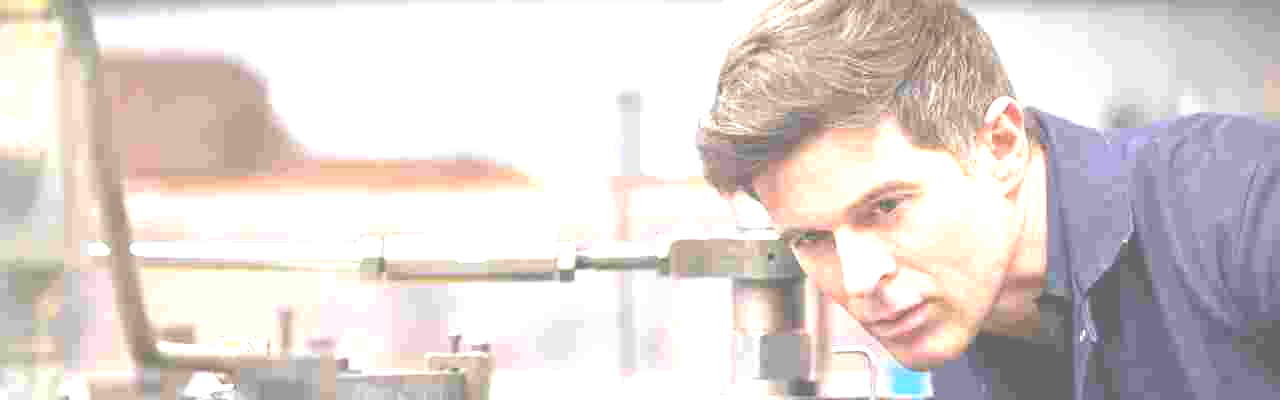

Калибры
Дополнительная информация по оборудованию: Калибры
- Описание
- Стоимость
- Примеры работ (фото, видео)
- Изготовители
- Применение
- ГОСТы
Разместить заказ
Выбрать исполнителя
Калибры в металлообработке: виды, применение и контроль точности
Калибры – это точные измерительные инструменты, которые применяются при производстве и обработке металлических деталей для контроля их соответствия заданным параметрам (размерам, формам, допускам). Они позволяют проверить, соответствует ли заготовка или деталь требуемым стандартам и чертежам без использования сложного измерительного оборудования.
Калибры широко применяются в машиностроении, приборостроении, авиа- и автомобильной промышленности и в целом везде, где критически важна точность обработки металла. Ниже мы подробно рассмотрим основные виды калибров, их назначение и принципы применения.
Основные функции калибров
- Контроль размеров. Главная задача калибров – проверка соответствия геометрических параметров детали заданным допускам: длине, диаметру, углу, форме и т. д.
- Стабилизация качества. Благодаря быстрой и объективной оценке размеров детали с помощью калибра, можно оперативно отслеживать и регулировать процесс производства, гарантируя стабильность качества выпускаемых изделий.
- Повышение производительности. При регулярном использовании калибров снижается количество брака и сокращается время на контроль – не требуется сложная разметка и дополнительный инструментальный контроль.
- Упрощение контроля на производстве. Рабочий или контролёр ОТК (отдела технического контроля) может оперативно проверить изделие на соответствие нужному допуску без сложных вычислений и измерений.
Основные типы калибров
Калибры бывают разных типов в зависимости от того, какой именно параметр детали необходимо проверять: внешний диаметр, внутренний диаметр, резьбу, профиль, геометрическую форму и т. д.
Проходные и непроходные (предельные) калибры
Проходной калибр (Go) служит для проверки того, может ли деталь «войти» в определённый размер. Если деталь соответствует верхнему предельному размеру (или нижнему, в зависимости от вида контроля), она должна свободно проходить в калибр.
Непроходной калибр (No-Go) проверяет другой предел допуска. Деталь не должна войти в непроходной калибр, если её размер не превышает заданного предельного значения.
Такая пара калибров (Go/No-Go) даёт быструю оценку: если деталь прошла в «проходной» калибр, но не вошла в «непроходной» – она признана годной. Если деталь не входит в «проходной» или входит в «непроходной», она не соответствует требуемым параметрам.
Штриховые (призматические) калибры
Используются для контроля линейных размеров, например, ширины паза или толщины детали. Калибр может представлять собой пластину или набор пластин (набор плоскопараллельных концевых мер), где точно выдержан требуемый размер.
Резьбовые калибры
Применяются для контроля резьб (наружной или внутренней). Резьбовой калибр-пробка (для внутренней резьбы) – цилиндр с нарезанной резьбой. Он должен легко «ввинчиваться» в проверяемое отверстие, если размер резьбы верный (Go), и не ввинчиваться (No-Go), если допуск нарушен. Резьбовой калибр-кольцо (для внешней резьбы) – кольцо с нарезанной резьбой, внутрь которого вкручивается проверяемый винт или болт. Аналогично: кольцо Go/No-Go позволяет определить годность резьбы.
Калибры-кольца (диаметральные)
Используются для контроля наружного диаметра вала, оси и т. д. Внешне напоминают сплошное кольцо с точно обработанной внутренней поверхностью. Принцип проверки схож с проходными/непроходными калибрами: если вал проходит в кольцо Go, это значит, что диаметр не превышает заданный допуск. Если при этом вал не проходит в кольцо No-Go, значит, он не выходит за нижний предел. Таким образом подтверждается соответствие детали необходимому размеру.
Калибры-пробки (для отверстий)
Предназначены для контроля внутреннего диаметра отверстий, их глубины, чистоты обработки и т. п. Это «цилиндры», внешний диаметр которых точно соответствует нужному размеру. Проходная пробка (Go) – должна заходить в отверстие, если оно соответствует минимально допустимому диаметру. Непроходная пробка (No-Go) – не должна полностью войти, если отверстие не превышает максимально допустимый размер.
Специализированные калибры
Иногда в машиностроении требуется проверять сложные профили (шлицевые, конические, фасонные и проч.). В таких случаях изготавливают специальные калибры по чертежам заказчика, которые точно повторяют заданную геометрию детали и позволяют контролировать её путём совмещения поверхностей.
Области применения калибров
Металлообработка и машиностроение. Контроль размерных параметров (вала, отверстия, резьбы) в процессе токарной, фрезерной, шлифовальной обработки и при сборке узлов. Ускорение процесса контроля в массовом производстве: при большом количестве деталей удобнее использовать готовый калибр, чем многократно проводить измерения штангенциркулем или микрометром.
Приборостроение и точное машиностроение. Требования к деталям здесь особенно высокие, поэтому калибры помогают поддерживать стабильное качество деталей с малыми допусками. Возможность быстрого контроля посадок (совпадение размеров отверстий и валов), что критически важно при сборке сложных механизмов.
Авиа- и автомобилестроение. Множество узлов и деталей (втулки, штифты, резьбовые соединения) должны строго соответствовать требованиям безопасности и надёжности. Контроль каждой партии деталей калибрами снижает риск брака, повышает точность сборки и облегчает обслуживание.
Металлургия и прокат. При выпуске металлопроката, сортового или фасонного проката (например, балки, швеллеры), калибры используются для проверки профилей, толщины и формы. Специальные калибры позволяют проверить соответствие геометрии проката техническим условиям и ГОСТам.
Судостроение и нефтегазовая промышленность. Контроль фланцевых соединений, фитингов и крепежа в условиях повышенных требований к герметичности и прочности. Применение резьбовых калибров для трубного крепежа (например, резьбы с коническим уплотнением).
Как правильно использовать калибры в металлообработке?
Убедитесь, что калибр чистый, без повреждений и соответствует требованиям точности. Хранить калибры рекомендуется в специальных футлярах или коробках, чтобы избежать попадания абразива и влаги. Перед использованием проверьте калибр на предмет коррозии или повреждений, способных исказить результаты контроля. Удалите с детали загрязнения, стружку, смазку, чтобы контакт поверхностей с калибром был корректным.
o
Если калибр проходной, деталь должна войти/выйти с лёгким натягом или без зазора (в зависимости от стандарта). При работе с непроходным она не должна входить целиком или не должна входить совсем (снова зависит от принятой системы допусков и посадок).
Со временем калибры изнашиваются, их размеры могут изменяться. Необходимо проводить регулярную поверку в аккредитованной лаборатории или на собственном метрологическом оборудовании. При обнаружении несоответствия или значительного износа калибр необходимо заменить или восстановить (для дорогих и специальных калибров делают ремонт/перешлифовку).
В серийном производстве каждый этап контроля часто сопровождается протоколами измерений и отметками о годности детали. При массовом контроле бывает достаточно отметки «годен»/«не годен», однако для ответственных деталей ведут более подробные записи.
Преимущества и особенности применения калибров
- Высокая скорость контроля. Использование проходных/непроходных калибров существенно ускоряет процесс проверки по сравнению с измерением универсальными инструментами (штангенциркули, микрометры и т. д.). Удобно при большом объёме деталей или в автоматических линиях (калибры могут устанавливаться в поточное оборудование).
- Стабильность и объективность результата. Нет необходимости в точной «ручной» регулировке измерительного инструмента: ответ «подходит/не подходит» очевиден. Минимальный риск ошибок, связанных с человеческим фактором (неправильная установка микрометра, неправильный отсчёт показаний).
- Низкая стоимость проверки. Хоть качественные калибры сами по себе могут стоить дорого, в перспективе они снижают брак и время простоя оборудования. Меньше расходуется время оператора, сокращается периодически необходимый дополнительный контроль.
- Ограниченность применения. Калибр, особенно предельный, рассчитан на конкретный номинальный размер и систему допусков. Для деталей других размеров потребуются иные калибры. Для универсального контроля сложных форм может потребоваться несколько наборов калибров, что увеличивает затраты.
Выбор и заказ калибров
Сначала нужно чётко понимать, какой параметр детали необходимо проверять: резьбу, диаметр, ширину, толщину, посадку и т. п. Исходя из этого выбирают между калибрами-пробками, калибрами-кольцами, резьбовыми калибрами и т. д. Существует множество стандартов (ГОСТ, DIN, ISO), каждая система допусков имеет собственные обозначения (например, 6g, 6H, 7H для резьбы и т. д.). Важно выбрать калибр в точном соответствии с допуском, указанным на чертеже детали.
Калибры обычно изготавливают из высококачественных инструментальных сталей (легированных, закалённых). Для повышения износостойкости применяется покрытие (типа хромирования). Для особо точных калибров могут использоваться твёрдые сплавы (но это чаще встречается в измерительных инструментов типа эталонных плит).
Хороший производитель калибров предоставляет сертификаты точности, калибры могут иметь государственную поверку. При заказе обратите внимание на репутацию производителя и сроки поставки.
Калибры – неотъемлемая часть современного металлообрабатывающего и машиностроительного производства. Они позволяют значительно упростить и ускорить контроль деталей, обеспечивая при этом высокую точность и объективность результатов. Правильно подобранный и своевременно поверенный калибр экономит ресурсы и время, снижает брак и помогает поддерживать стабильное качество продукции.
Используя калибры грамотно и регулярно, можно:
- оптимизировать процессы проверки на предприятии,
- сократить затраты на контроль и повысить общую производительность,
- усилить конкурентные преимущества за счёт выпуска более качественных деталей и изделий.
При выборе калибра важно учитывать не только номинальные размеры и допуски, но и условия эксплуатации (интенсивность использования, температурный режим, требования к точности). В совокупности эти факторы позволяют организовать эффективную систему контроля качества и достичь стабильного результата при обработке металла.
Тип калибра | Стоимость, тыс. руб. | |||
---|---|---|---|---|
Цилиндрическая пробка гладкая |
от 3 | |||
Цилиндрическая пробка ступенчатая | от 5 | |||
Кольцо гладкое | от 4 | |||
Скоба | от 6 | |||
Пробка резьбовая | от 6 | |||
Кольцо резьбовое | от 7 | |||
Профильный калибр | от 10 | |||
Калибр для контроля углов | от 8 | |||
Калибр для контроля расстояний | от 7 | |||
Калибр для контроля канавок и пазов | от 9 | |||
Конусная пробка | от 7 | |||
Конусное кольцо | от 8 |
Автор данного ролика представлен в нашем каталоге:
_