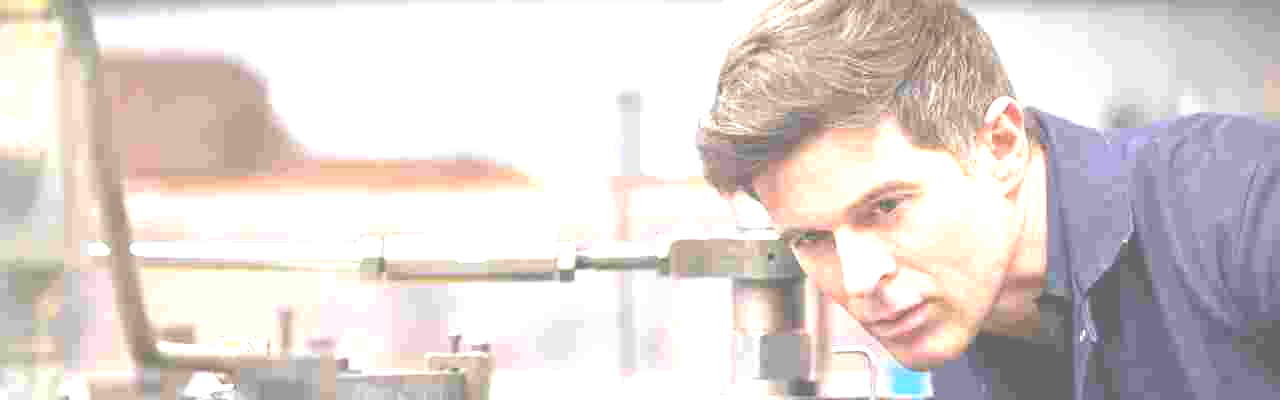

Магнитные дефектоскопы
Дополнительная информация по оборудованию: Магнитные дефектоскопы
- Описание
- Стоимость
- Примеры работ (фото, видео)
- Изготовители
- Применение
- ГОСТы
Разместить заказ
Выбрать исполнителя
Магнитные дефектоскопы: принципы работы, виды
и применение в неразрушающем контроле
Магнитные дефектоскопы – оборудование, предназначенное для обнаружения поверхностных и подповерхностных дефектов (трещин, пор, непроваров и др.) в деталях из ферромагнитных материалов. Технология магнитной дефектоскопии широко применяется в металлургической промышленности, машиностроении, судостроении, авиации и других отраслях, где необходим строгий контроль качества металла и сварных соединений.
Ниже рассмотрим основные принципы работы магнитных дефектоскопов, их виды, возможности и особенности применения.
Принцип работы магнитных дефектоскопов
В основе работы магнитных дефектоскопов лежит явление магнитного рассеяния. Если деталь намагничена и в её структуре присутствует дефект (трещина, раковина и т. д.), в районе этого дефекта магнитное поле искажается. Когда на деталь наносится магнитный порошок или магнитная суспензия, частицы концентрируются в местах неоднородности магнитного поля, визуально выявляя зону дефекта.
Существует несколько способов намагничивания:
- продольное (через катушку или соленоид);
- поперечное (с помощью электрического тока, пропущенного через деталь);
- местное. Наиболее распространено для ручных приборов, когда переносной магнит накладывается на участок контролируемой поверхности).
В процессе нанесения магнитеого состава используются магнитные порошки или суспензии (порошок + жидкий носитель). Частицы данного состава ферромагнитны и собираются в местах утечки магнитного поля. После нанесения состава оператор (или автоматическая система) проводит визуальный осмотр. Если есть трещины, непровары или поры, на месте дефекта образуются “индикаторные полосы” или скопления порошка.
Виды магнитных дефектоскопов
Существует несколько основных типов магнитных дефектоскопов, различающихся способом намагничивания детали, конструкцией и областью применения.
Стационарные установки
Используются в условиях крупного производства (цеха, заводы) для массового контроля деталей. Позволяют намагничивать детали разными способами (продольное, поперечное намагничивание, импульсное и др.) и работать с крупногабаритными заготовками. Могут быть полностью автоматизированными, что повышает производительность и снижает влияние человеческого фактора.
Переносные (ручные) магнитные дефектоскопы
Применяются при выездном контроле (в полевых условиях, на строительных площадках, при ремонте трубопроводов и т. д.). Имеют компактные размеры и относительно небольшой вес, что облегчает использование. Позволяют проводить локальное намагничивание определённого участка детали, что удобно для обследования труднодоступных мест.
Специализированные системы
Создаются для решения конкретных задач, например, для контроля труб, рельсов, сварных швов и т. д. Часто имеют модульную конструкцию, позволяющую адаптировать их под разные типоразмеры и формы изделий.
Используемые вспомогательные материалы
При магнитном контроле применяются специальные расходные материалы, которые помогают “проявить” скрытые дефекты:
- магнитные порошки. Сухие порошки разных цветов (чёрные, цветные, флуоресцентные). Хорошо видны при контроле в нормальном и ультрафиолетовом свете. Используются, когда поверхность детали относительно ровная и доступна для визуального осмотра;
- магнитные суспензии. Представляют собой смесь мелкодисперсных ферромагнитных частиц с жидким носителем (вода, масло или другие специальные жидкости). Нанесение суспензии удобно для деталей сложной формы или при необходимости быстрого покрытия большой площади. Флуоресцентная суспензия особенно эффективна при контроле в ультрафиолетовом свете, так как даёт контрастное свечение в зоне дефекта;
- средства для предварительной очистки и защиты. Перед намагничиванием поверхность детали очищают от загрязнений, ржавчины и масел, иначе точность контроля снижается. После контроля иногда используют специальные антикоррозионные составы, чтобы защитить металл от окисления.
Технологические этапы контроля
Процесс контроля магнитным дефектоскопом можно разделить на несколько шагов:
- Подготовка детали. Очищают поверхность, снимают старое покрытие (краску, лак), удаляют загрязнения и масляные отложения. Проверяют пригодность материала к магнитному контролю (деталь должна быть из ферромагнитного сплава);
- Выбор и настройка режима намагничивания. Определяют оптимальную силу и направление магнитного поля. o Учитывают конфигурацию детали и предполагаемые направления дефектов;
- Намагничивание и нанесение выявляющего состава. Продольное или поперечное намагничивание, в зависимости от поставленной задачи. Распыляют или наносят кистью/распылителем магнитный порошок или суспензию;
- Осмотр и фиксация результатов. Визуальный контроль с использованием обычного или ультрафиолетового освещения (при флуоресцентном методе). Фото- или видеорегистрация выявленных дефектов. Анализ полученных данных и их документирование;
- Размагничивание. После завершения контроля деталь размагничивают (особенно если она будет работать в условиях, требующих отсутствия остаточной намагниченности). Применяют технологию обратного поля или используют специальные размагничивающие установки.
Преимущества и ограничения магнитного контроля
Метод позволяет выявлять даже мельчайшие трещины, невидимые невооружённым взглядом. Операция контроля занимает относительно мало времени, особенно на автоматизированных комплексах. Расходные материалы (порошки, суспензии), а также сами магнитные дефектоскопы (особенно ручные) стоят сравнительно недорого по сравнению с некоторыми другими методами неразрушающего контроля. Дефекты проявляются визуально, оператор чётко видит их форму и расположение.
Но для этой технологии существуют и ограничения. Нельзя проверить алюминий, магний, латунь или нержавеющую сталь с низкой магнитной проницаемостью. Метод не подходит для закрытых полостей и внутренних дефектов на большой глубине. Наличие ржавчины, слоя краски или сильных загрязнений искажает результаты. В ряде случаев остаточная намагниченность может быть недопустимой.
Области применения
Магнитные дефектоскопы широко используются в различных отраслях промышленности:
- металлообработка и машиностроение. Контроль валов, шестерён, осей, деталей двигателей. Проверка сварных соединений на предмет непроваров и трещин. Диагностика заготовок и полуфабрикатов перед окончательными операциями (закалка, финишная обработка и т. п.);
- нефтегазовая отрасль. Регулярный осмотр трубопроводов, насосных станций, резервуаров. Выявление усталостных трещин и предупреждение аварий;
- судостроение и судоремонт. Контроль корпусных конструкций и сварных швов на кораблях. Проверка редукторов, винтов, валов и других ответственных механизмов;
- авиация. Инспекция шасси, элементов фюзеляжа, рабочих лопаток турбин и т. д. Контроль критически важных узлов, от которых зависит безопасность полётов;
- железнодорожный транспорт. Диагностика рельсов, колёсных пар, осей. Быстрое выявление трещин, возникших из-за динамических нагрузок и перепадов температур.
Тенденции развития и инновации
Современные тенденции в области магнитной дефектоскопии направлены на повышение точности и автоматизацию процессов. Автоматизированные установки могут делать снимки (цифровые фотографии или видео) и на основе программного анализа выявлять дефекты, что снижает субъективность операторской оценки. Для контроля крупных объектов (резервуаров, трубопроводов) всё чаще применяются роботы, которые перемещаются вдоль поверхности и проводят намагничивание и съём данных.
Магнитный контроль часто сочетается с ультразвуковым, вихретоковым и другими методами, что даёт более полную картину состояния детали. Современное оборудование отличается меньшим весом, улучшенной системой охлаждения и удобными интерфейсами. Внедряются новые материалы и разработки, снижающие риски для оператора и окружающей среды.
Магнитные дефектоскопы – один из самых востребованных инструментов неразрушающего контроля в металлургии, машиностроении и других отраслях. Их простота, наглядность и относительная дешевизна делают этот метод незаменимым при выявлении трещин, непроваров и других поверхностных дефектов в ферромагнитных деталях.
При грамотном выборе типа дефектоскопа и правильной организации технологических процессов можно существенно повысить надёжность и долговечность оборудования, минимизировать риски аварий и получить экономию за счёт снижения брака и своевременного ремонта.
Тип дефектоскопа | Стоимость, тыс. руб. | |||
---|---|---|---|---|
Ручные магниты (скобы, “копытца”) |
от 5 | |||
Переносные электромагниты (AC/DC) | от 30 | |||
Стационарные магнитные установки (горизонтальные) | от 500 | |||
Стационарные магнитные установки (вертикальные) | от 700 | |||
На постоянных магнитах (для труб) | от 50 | |||
Магнитные головки для автоматизированных линий | от 200 | |||
Приборы для измерения характеристик магнитного поля | от 50 |
Автор данного ролика представлен в нашем каталоге:
_